Heavy Fabrication Company in Delhi
Cyclotron is the leading heavy fabrication company in Delhi. With decades of experience in welding and commitment to quality, we provide top notch heavy fabrication services tailored to meet your requirements. Our advanced fabrication techniques and skilled workforce ensure that every project we undertake is completed with highest standards, delivering the desired outcome.
Heavy fabrication services in Delhi
At Cyclotron we offer a comprehensive range of heavy fabrication services in Delhi. Whether you need a custom built structure, complex parts, automotive parts, construction equipment, etc we are here to cater all your welding needs. We make use of cutting edge technology for providing fabrication services like
- Heavy & Medium fabrication
- Advanced Robotic welding
- Welding fixtures
- Welding Positioners
- Welding tables and clamping systems
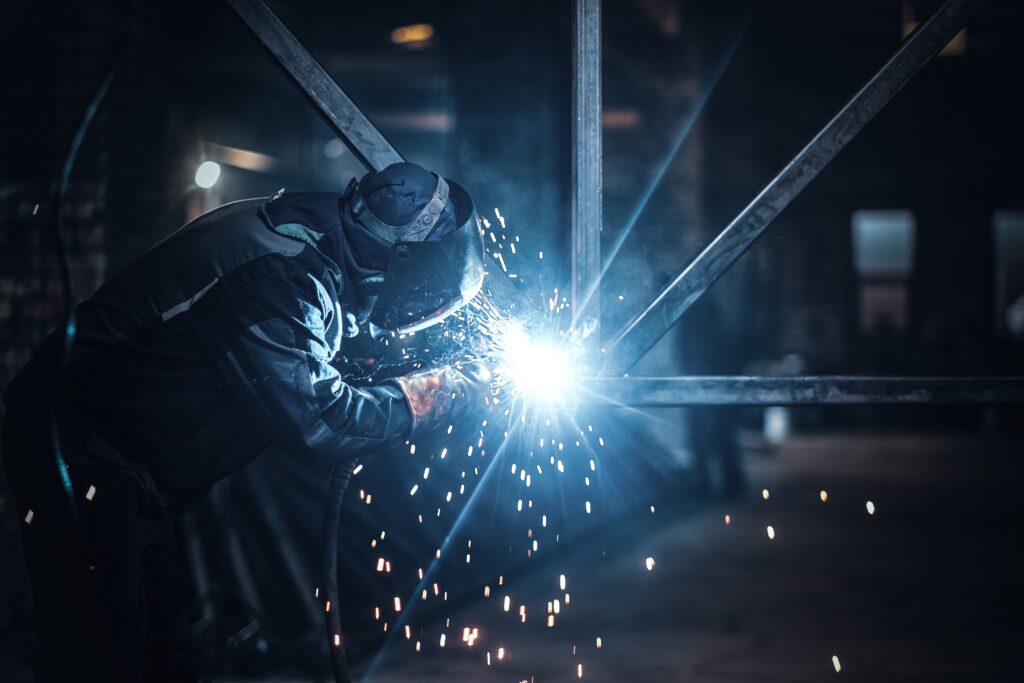
Why choose our fabrication services in Delhi?
Choosing the right heavy fabrication partner for your project is important because it will have a long term impact on the quality of your products and manufacturing. At Cyclotron, we offer top fabrication services in Delhi to meet diverse needs of all the complex requirements you have, ensuring the best quality of every project delivered. We use a combination of advance technology and skilled welders to ensure your projects have the best fabrication quality and deliver it in the best
Reliable Supplier
Once you have choosen us as our fabrication supplier, you need to be rest assured of the quality of the products and timely delivery.
Cost Effective
We offer the most affordable prices in the market with a greater assurance of the best quality of work to be delivered.
Lowest Lead time
We make use of latest automation technologies to insure your products get delivered to you within the least possible time.
Quality Assurance
Use of enhance quality techniques and SOPs defined will assure your products to have the desired quality.
Industries we serve
Cyclotron offers heavy fabrication services in all types of industries including renewables, aerospace, automotive, construction, general fabrication , etc. Our expert team of engineers, welders and technicians make sure that your products be it in ay of the above industry is up to the mark as per the industry standard.
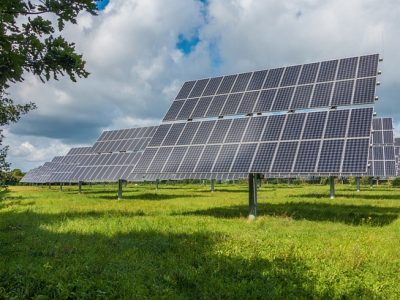
Renewable Energy
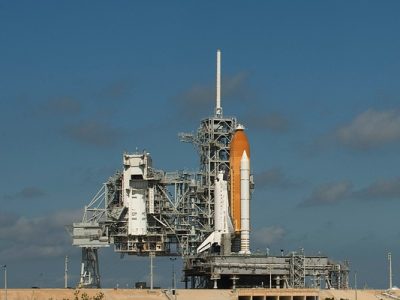
Aerospace Industry
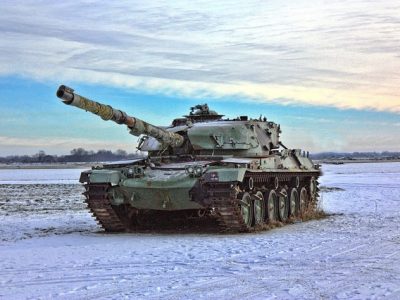
Defence Industry
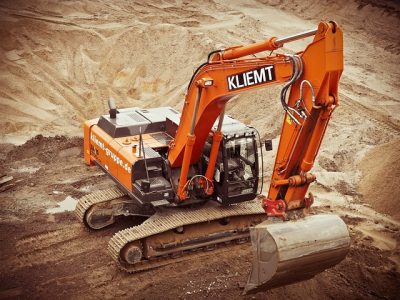
Construction Industry
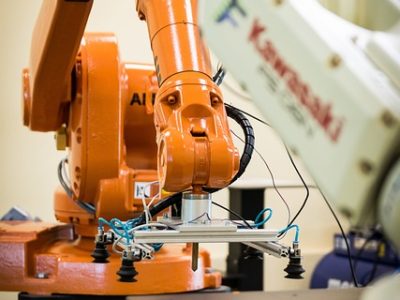
Automation Industry
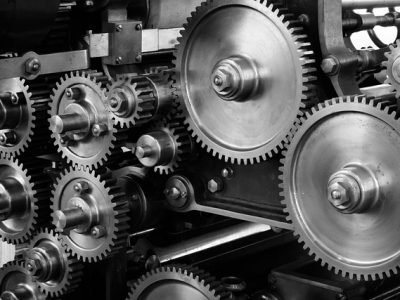
Automotive Industry
Safety and quality standards
Quality Assurance process: Quality is embedded in every stage of our fabrication process. From material selection to final inspection, we follow a systematic approach to ensure that every product meets the highest standards of quality.
Material selection and quality testing: We source high-quality raw materials that meet industry specifications and client requirements. These materials undergo testing to ensure they possess the necessary strength and ductility.
Inspection protocols: We have several inspection points throughout the fabrication process, where each product is checked for compliance with design and quality standards
Precision fabrication: Utilizing advanced technology and skilled welders we ensure to meet top notch quality in every step of fabrication. They are designed to maintain tight tolerances, and precision.
Final Product testing: Before delivery every product undergoes final testing to ensure it meets all safety and quality criteria.
Robotic welding fixture with positioner in Delhi
Truck trailer fabrication using Welding positioner
Tooling fixture for fabrication in Delhi
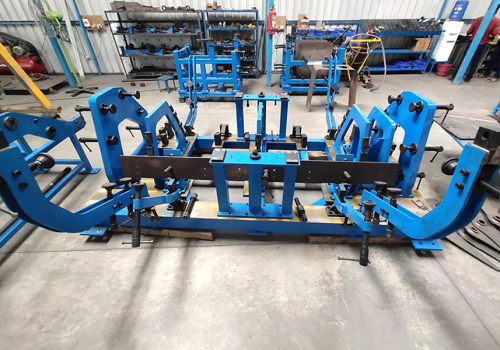
Loader Bucket Welding fixture
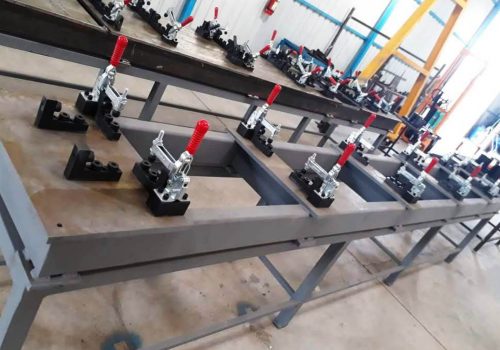
BIW Welding fixture
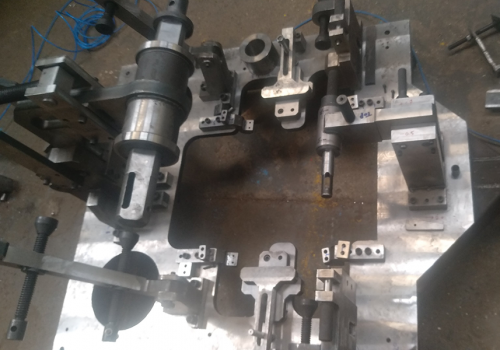
Axle Support Welding fixture
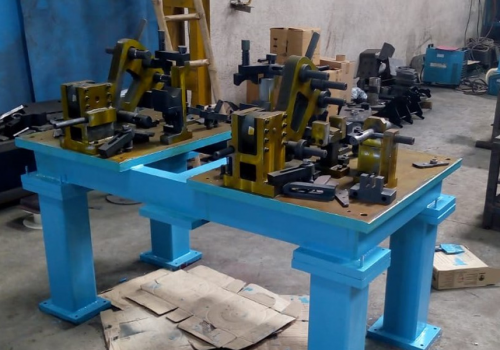
Slider assembly
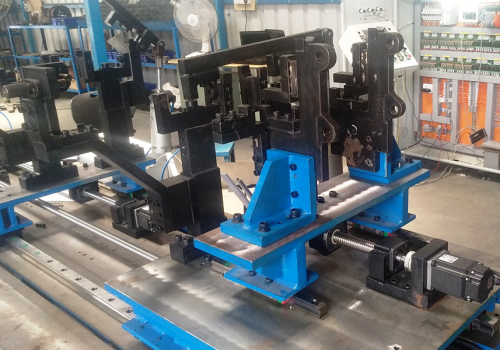
welding fixture
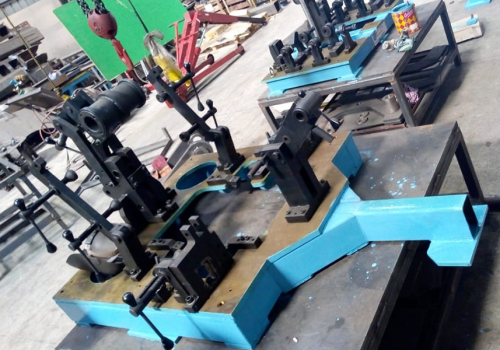
Pivot assembly
Customers List
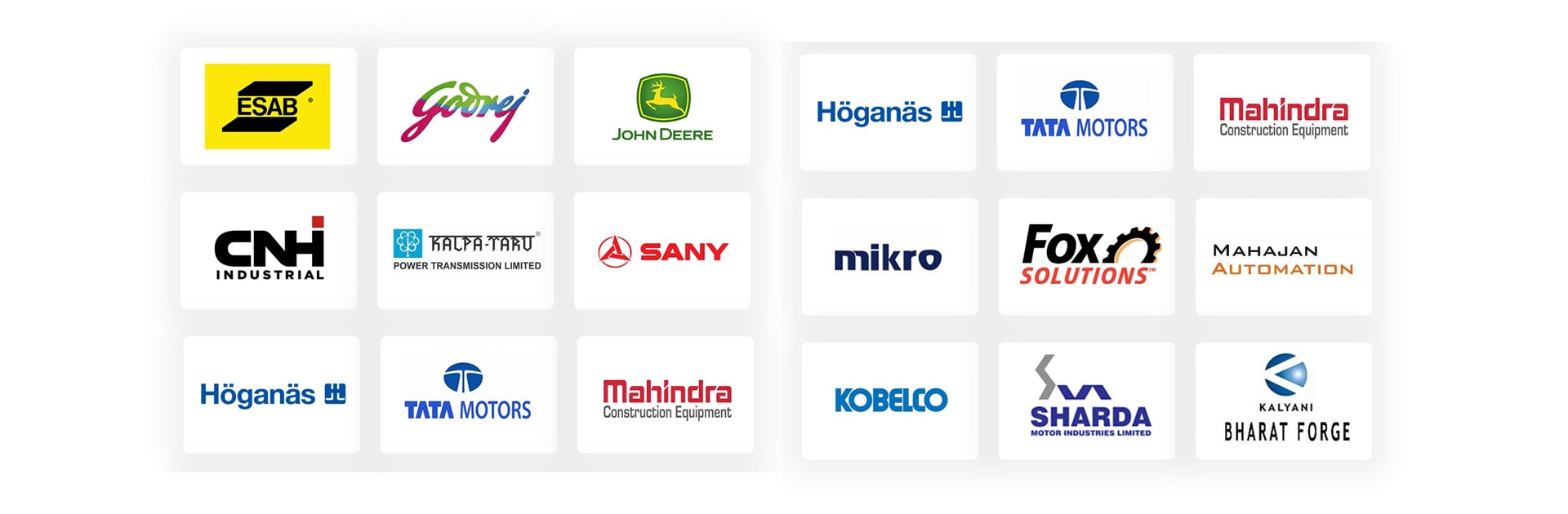
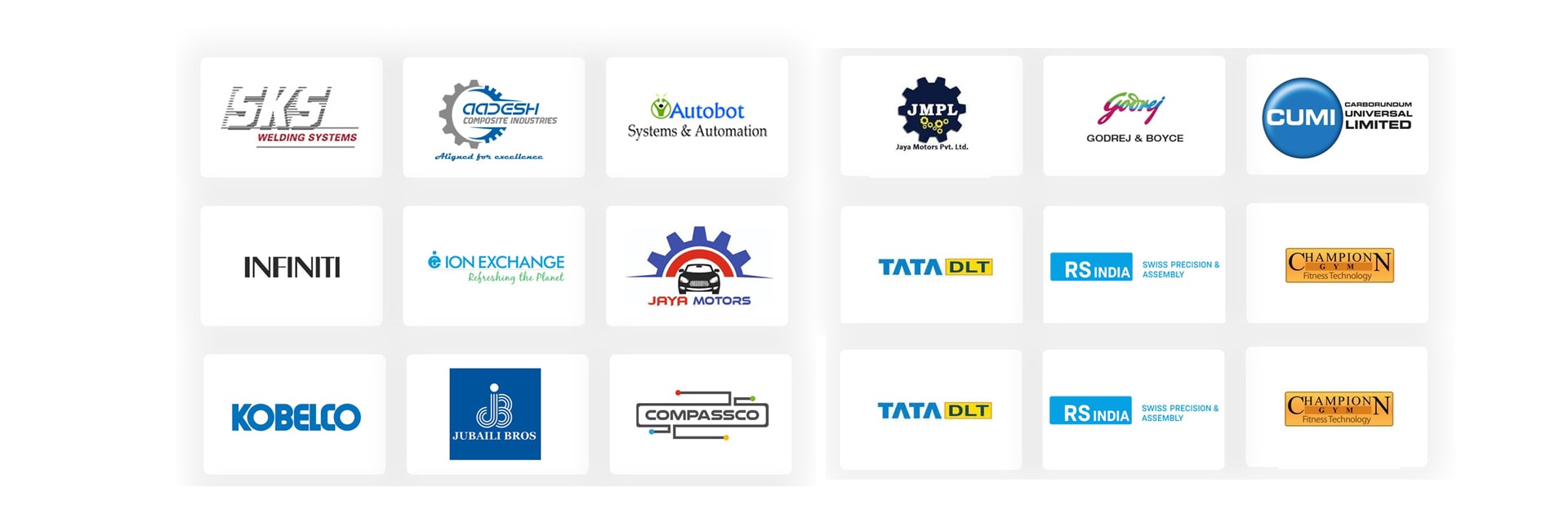
Our steel fabrication process
Large fabrication projects require a proper planning and execution of the projects to ensure a smooth delivery of the project. It involves various steps as follows
- Cutting:
- Cutting is the most important and critical step in any fabrication process.
- It involves shaping of raw materials into required dimensions and forms, which will be assembled into the final product.
- Accurate cutting is important for the quality of the end product which will be manufactured
Process of Cutting:
- Material selection: The type of material being cut decides which cutting technique will be used.
- Cutting techniques: Includes Plasma cutting, laser cutting, water jet cutting, and oxy fuel cutting. Technique is used based on the material selected, thickness, precision required, etc
- Tolerance: High accuracy is needed in this step, as minor issues in this step will lead to larger failures in the next steps
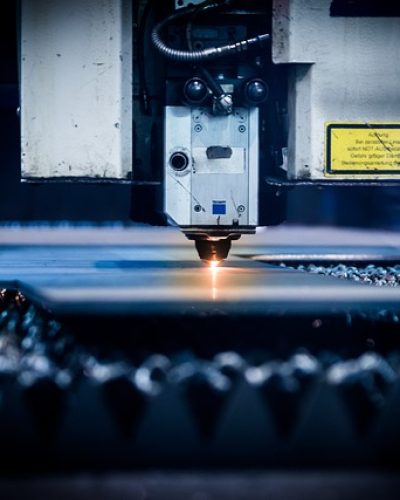
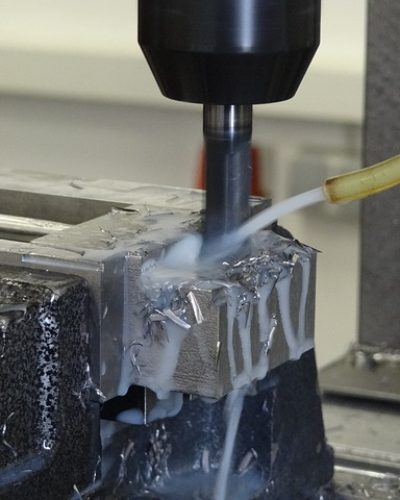
2. Drilling:
- Used to create holes in metal components which are used for assembly, mounting or other functionality.
Process of drilling:
- Tool selection: Type of drill bit and drilling method depends on the material being worked on and required size and depth of the hole. High speed steel and carbide bits are commonly used.
- Accuracy: Accurate positioning of holes is necessary, as misaligned holes can compromise the quality. Jigs and Cnc machines are used for drilling
- Coolant use: The coolant is used to avoid overheating of the part and the drill.
3. Bending:
- Bending involves deforming of cut metals into desired structures without breaking it.This is used to form angles, structures, complex geometries, etc.
Process of bending:
- Bending methods: Common bending techniques include press braking, roll bending, and rotary draw bending. The method chosen depends on the material type, thickness, and the bend radius required.
- Spring back compensation: Some metals tend to go to their original positions even after bending, to avoid this spring backs necessary precautions are taken care of.
- Tooling: Selection in tooling such as dies and punches is critical in achieving the desired bend without cracks.
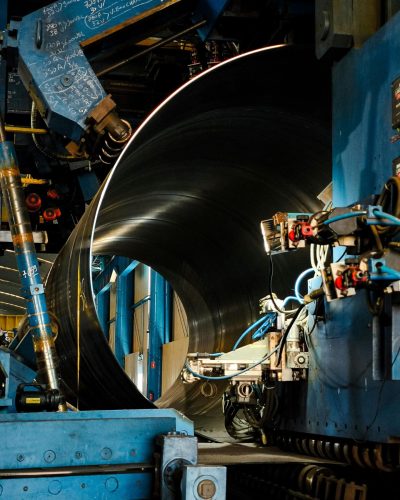
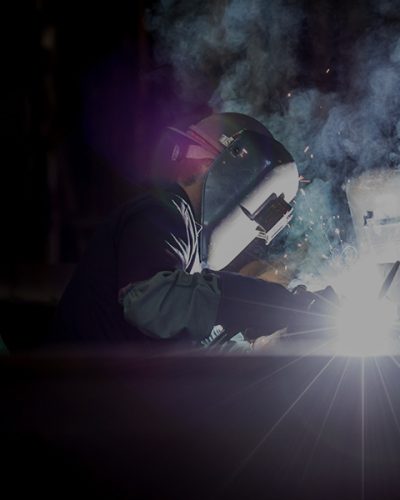
4. Welding:
- It is the process of joining two metal parts to form a single structure. It is one of the most critical stage in fabrication, as quality of weld directly affects the product strength.
Process of welding
- Welding techniques: Various welding methods are used in fabrication, including MIG (Metal Inert Gas), TIG (Tungsten Inert Gas), and stick welding. The choice of method depends on the materials, thickness, and specific project requirements.
- Weld quality: Achieving high quality welds are super important for the overall structural integrity. Factors such as weld penetration, bead appearance, and joint strength are carefully monitored.
- Automation: Advanced welding automation systems, such as robotic welders, are increasingly used in large fabrication projects to enhance precision, consistency, and efficiency
- Painting:
- Painting is the final step of the fabrication process providing an aesthetic look to the product as well as a coating for being the resistive layer for products.