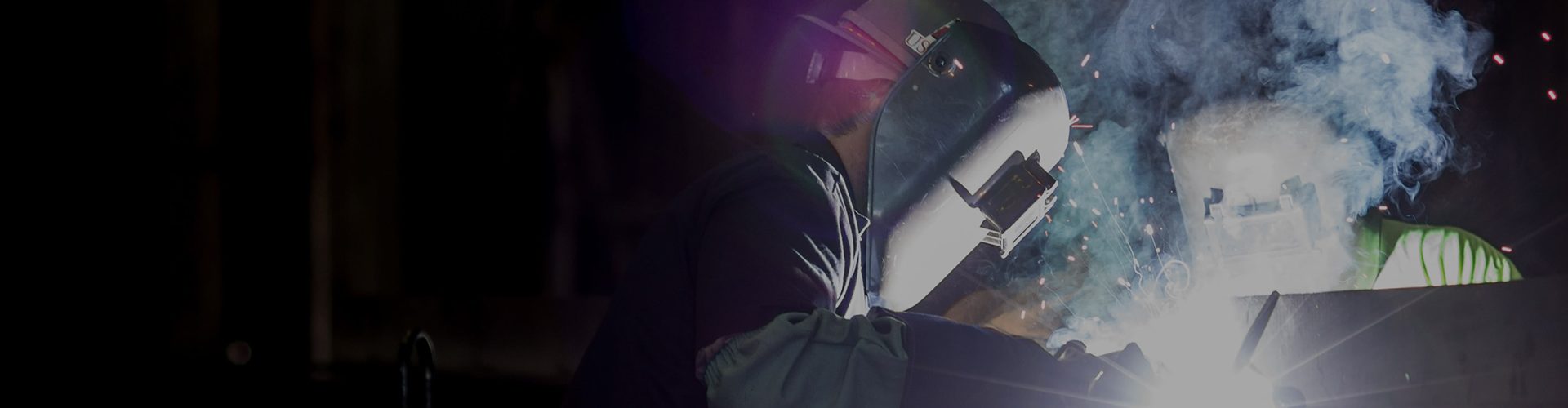
BLOGS BY CYCLOTRON
TYPES OF WELDING FIXTURES
The main purpose of a fixture is to locate, support and hold the workpiece in position firmly to obtain a precise product from a process.
A welding fixture is designed in a way to support and locate the components to be welded to avoid distortions and weld stresses. It is obvious that each welding operation requires a distinct welding fixture according to our desired requirements. A fixture generally holds the part during welding, but there is a chance of the part being distorted after the removal of the fixture. Hence some stress-relieving and other post-processing operations can be performed to prevent weld distortions.
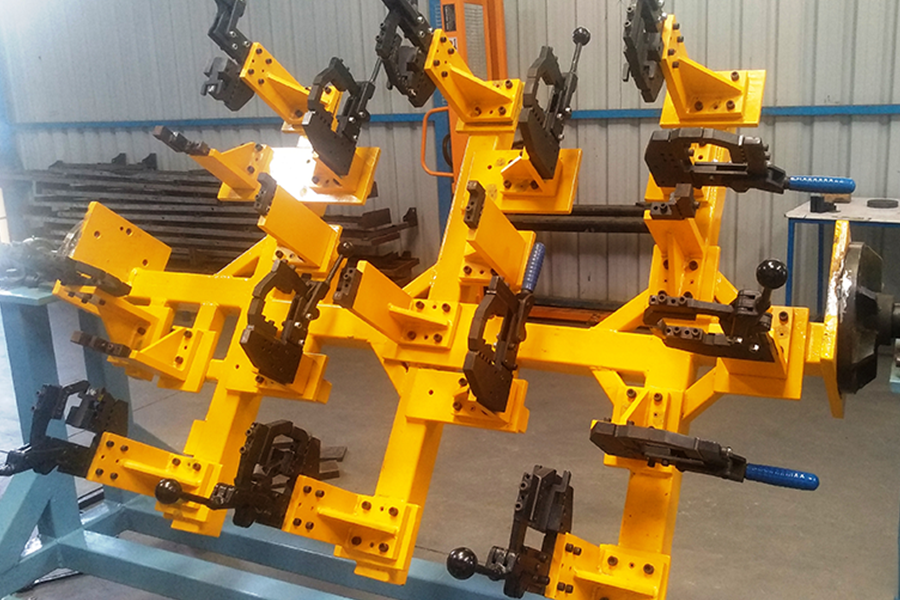
1. Gas Welding Fixtures
Welding is done by burning fuel in the presence of oxygen which produces extremely high temperatures that melt the parts and join them during welding. In the case of gas welding, the heat loss should be minimum to avoid weld cracks. Hence fixtures should be designed in such a way that large fixture masses are located away from the weld line while providing enough support to the workpieces.
Special care is required while welding copper and aluminium due to excessive heat loss from the materials. To address this difficulty, tack welding has to be done on the points away from the fixture contact points and the rest of the welding is done out of fixtures. C-clamps and hold down plates are additionally used to support the workpiece and prevent weld distortions.
2. Arc Welding Fixtures
The workpiece can react chemically with oxygen and nitrogen gases from the air at higher temperatures produced by the arc while welding. To prevent the part from reacting with air, a protective shielding gas is used around the welding area to minimise the exposure of the workpiece to the surroundings.
The temperatures produced in arc welding are much higher than those in gas welding. Hence they are used in welding steel structures and vehicles. More heat is generated at the weld line in arc welding than that of gas welding. Therefore the fixture, in this case, should provide good support, proper alignment to the workpiece and also allow heat dissipation from the weld area.
They should provide enough force to align the workpiece firmly. This force is applied at suitable points by clamps supported by backing bars. These backing bars not only provide robust support to the molten metal but also shield them from distortion.
3. Resistance Welding Fixtures
The fixtures must be free of debris and flash for safe operation. There are various reasons for healing up of the fixture like inductance, insulation, weld flash and location. Even magnetic tooling causes similar issues. The tool absorbs energy and heats up during welding which forces the welder to work harder for spot welding. To avoid this, fixtures, base plates and other components are made from non-magnetic materials.
Insulate fixture to prevent current flowing through it and heating up due to resistance heating. From bolts to mating surfaces, insulate all the components of the fixture.
4. Laser Welding Fixtures
Laser welding is known for its versatility and quickness in producing narrow, deep welds with a minimum distortion and heat input. It has gained much popularity among the parts that require little to no-post weld processing. Also, laser welding with a proper fixture eases the tool work, results in a precise product in less time.
A high-intensity laser beam is focused on the part to be welded using a lens. It melts the material and fusion welding takes place due to the intense heat produced. The fixture should be designed such that the laser is placed on a firm mounting to prevent vibration.
Sufficient space is allowed between work table and lens to in-house various positioning tools. When more than one fixture has to be used, control the working heights of both the fixtures with respect to each other to prevent accidental defocusing that may result in poor quality.
In a word, a fixture is the one that makes work easier for tools, reduces lead time, improves productivity and quality of the welded parts without any distortion. A different fixture is designed for different welding operations. There are Robotic welding fixtures to perform automatic welding, BIW welding fixtures, Lift and Weld fixtures, frame fixtures, railing weld fixtures etc each one with each purpose. We shall go through each of them in the upcoming articles.
NEED A WELDING FIXTURE ?
We at Cyclotron Robotics and Automation Pvt. Ltd. manufacture all types of welding fixtures as per your requirement.