Tips to improve welding productivity
How To Improve Welding Productivity Using Welding Positioner
Welding is all about precision, efficiency, and consistency. In industries where every weld counts, even small inefficiencies can lead to significant time and cost overruns. The secret to maximizing welding productivity lies in optimizing how the workpiece is positioned. A welding positioner is a game-changer, allowing operators to rotate, tilt, and secure workpieces effortlessly. By eliminating frequent manual adjustments and unnecessary movements, a welding positioner can boost productivity by up to 70%, ensuring faster, safer, and more accurate welds.
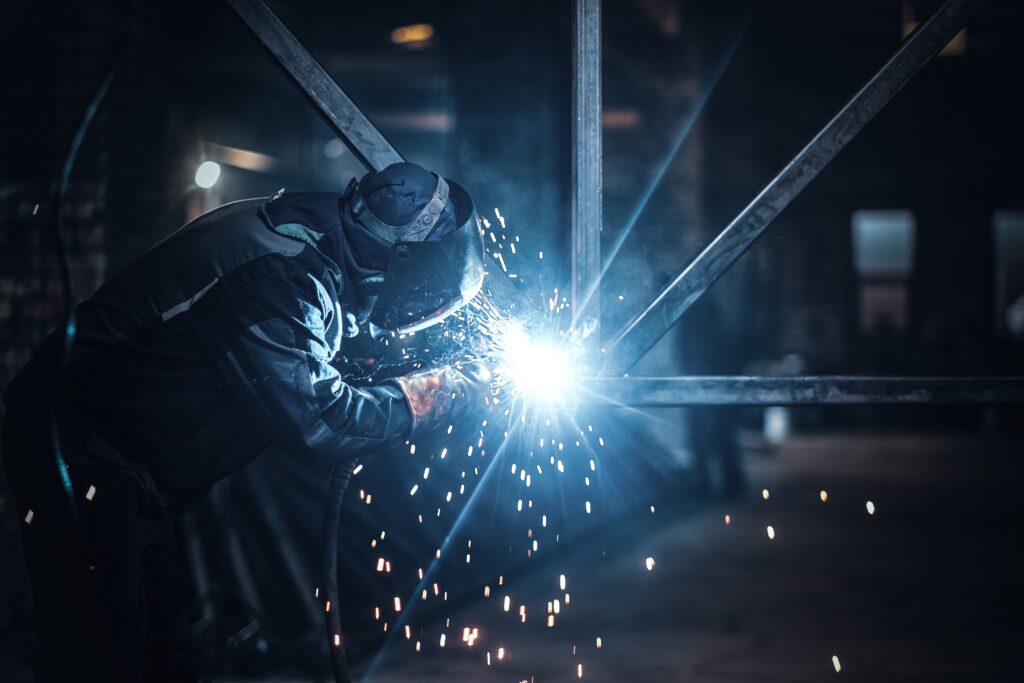
Benefits of Welding Positioners
Want to make the most out of your welding operations? Here’s how to improve welding productivity using a welding positioner.
1. Reduce Welding Time
Manually adjusting and aligning workpieces is time-consuming. It may take multiple trial-and-error attempts before achieving the right welding position. A welding positioner allows operators to position and secure the workpiece quickly, minimizing downtime and boosting welding productivity.
- Eliminates Repetitive Adjustments: With manual setups, welders often spend time rotating and repositioning parts. A welding positioner automates this, reducing unnecessary movement.
- Streamlines Multi-Pass Welding: For thick materials that require multiple passes, a positioner ensures smooth transitions between passes, minimizing delays.
- Faster Setup for Different Jobs: Welding positioners allow for quick adjustments between different jobs, ensuring an uninterrupted workflow.
2. Enhance Welding Precision
Industries such as shipbuilding, defense, and construction require high-precision welding. A positioner for welding with automated features reduce manual intervention, improve weld accuracy, and ensure high-quality welds while lowering overall costs.
- Minimizes Human Error: With consistent positioning, welders can focus on precision rather than adjusting the workpiece.
- Reduces Weld Defects: Proper alignment ensures better penetration, reducing the chances of cracks, porosity, or weak joints.
- Ensures Consistent Welds: Automated positioners enable uniform weld quality across multiple components, making mass production more efficient.
3. Improve Operator Safety
Welding-related musculoskeletal injuries are common, affecting the back, neck, shoulders, and wrists. A positioner reduces the need for excessive physical effort, preventing injuries and reducing operator fatigue. Additionally, it minimizes welding errors caused by exhaustion or inexperience.
- Reduces Heavy Lifting: Manual handling of large workpieces increases the risk of injuries. Positioners eliminate the need for excessive movement and lifting.
- Provides a Stable Work Environment: Welding positioners provide a secure and steady platform, preventing accidents caused by unstable setups.
- Lowers Fatigue-Related Errors: A comfortable working position allows welders to focus on precision rather than managing physical strain.
4. Select the Right Welding Positioner
Different welding tasks require different positioners. Choose based on workpiece size, weight, and movement requirements:
- Motorized Welding Positioners – Ideal for high-precision welding operations in industries like aerospace and automotive manufacturing.
- Turntable Positioners – Perfect for circular welds, often used in pipe welding and pressure vessel fabrication.
- Tilting Positioners – Best for complex angles, providing flexibility for intricate welding applications.
- Headstock & Tailstock Positioners – Suitable for long and heavy workpieces, ensuring balanced support during welding.
5. Optimize Operator Ergonomics
Without a positioner, welders must adjust their position frequently, leading to fatigue and errors. A welding positioner provides a stable, ergonomic setup, reducing unnecessary movements and ensuring consistent, high-quality welds.
- Reduces Unnecessary Movements: Welders no longer have to walk around the workpiece to adjust angles manually.
- Enhances Comfort & Focus: A stable work environment improves the welder’s ability to concentrate on the weld, leading to fewer mistakes.
- Lowers Physical Strain: By positioning the workpiece at an optimal height and angle, welders can maintain a natural posture, reducing strain on their body.
6. Monitor and Maintain Regularly
Setting up the right welding positioner is just the first step. Continuously monitor welding speeds, cycle times, and overall weld efficiency. Regular maintenance helps prevent breakdowns and maximizes productivity.
- Track Welding Parameters: Monitoring speed, heat settings, and rotation times help identify inefficiencies and optimize performance.
- Inspect Welding Equipment Regularly: Routine checks on motors, gears, and clamps ensure smooth operation and prevent unexpected failures.
- Lubricate Moving Parts: Regular lubrication reduces wear and tear, extending the lifespan of the positioner.
- Train Operators for Maintenance: Educating welders on basic troubleshooting helps prevent downtime and keeps operations running smoothly.
7. Use Proper Welding Techniques
A welding positioner enhances productivity, but correct welding techniques are still essential. Operators should be trained in torch angles, speed, heat settings, and cycle times. Integrating positioners with robotic welding systems can further automate processes, ensuring consistent and uniform welds.
- Train Operators on Welding Methods: Using proper filler materials and heat control can improve weld strength and appearance.
- Implement Automation Wherever Possible: Positioners combined with robotic arms enhance efficiency in large-scale production.
- Use Consistent Welding Parameters: Standardizing settings for similar jobs ensures uniform results and reduces errors.
- Minimize Spatter and Waste: Proper positioning leads to cleaner welds, reducing post-weld cleanup time.
Choose the Right Welding Positioner for Your Needs
Welding positioners are transformative tools that can revolutionize your welding operations. Do you want to upgrade your equipment? Or start a welding business? These devices enhance weld quality, increase efficiency, and reduce labor costs. This results in higher productivity, flawless welds, and improved customer satisfaction, driving greater profits.
Ready to find the best welding positioners for sale in India? At Cyclotron Automation, we provide technologically advanced, durable welding positioners that elevate Indian standards to a world-class level. Our intuitive interface allows operators to quickly learn and master the use of welding positioners. As a result, they work with more confidence, experience less fatigue, and maintain greater focus—ultimately boosting weld quality.
Upgrade today and weld with precision and efficiency!
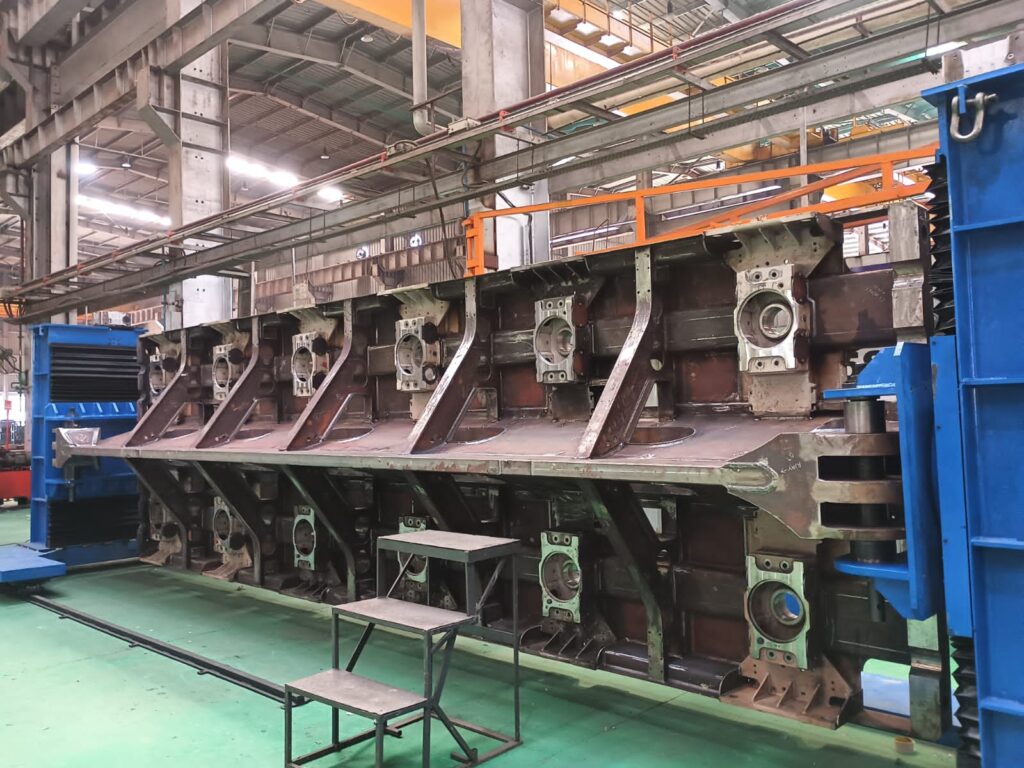
Looking for a reliable Welding Positioner?
Contact us at +91 9881217196
OR
Fill this form and our representative will get back to you.
Countries we Export to
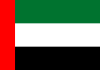
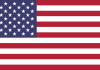
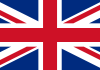
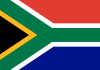
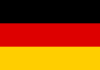
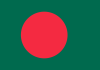
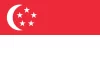
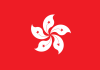
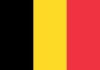
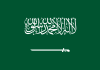
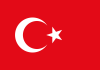
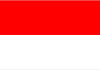
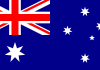
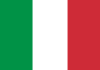
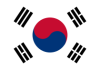
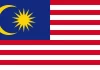

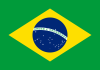
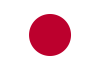
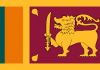
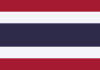
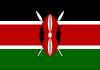
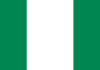
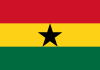