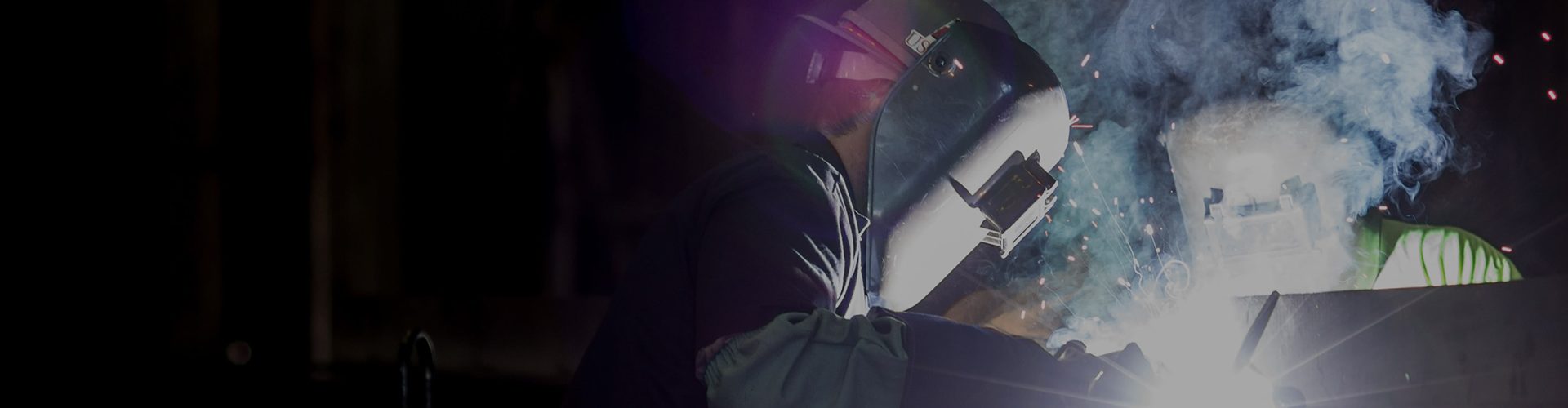
BLOGS BY CYCLOTRON
SHIELDING GASES FOR WELDING
Why Shielding is required during Welding?
While welding any metal or a component, the high temperatures produced during the process melts the material and a molten metal weld pool is formed. The atmosphere is a mixture of gases that can enter the weld pool and react with it causing a variety of issues like porosity, excessive weld spatter, poor weld quality. It severely affects the final quality of the product. Thus, some arrangement is necessary to protect the weld pool from the atmospheric gases but it shouldn’t react with the molten metal. This purpose is fulfilled by the provision of shielding gases
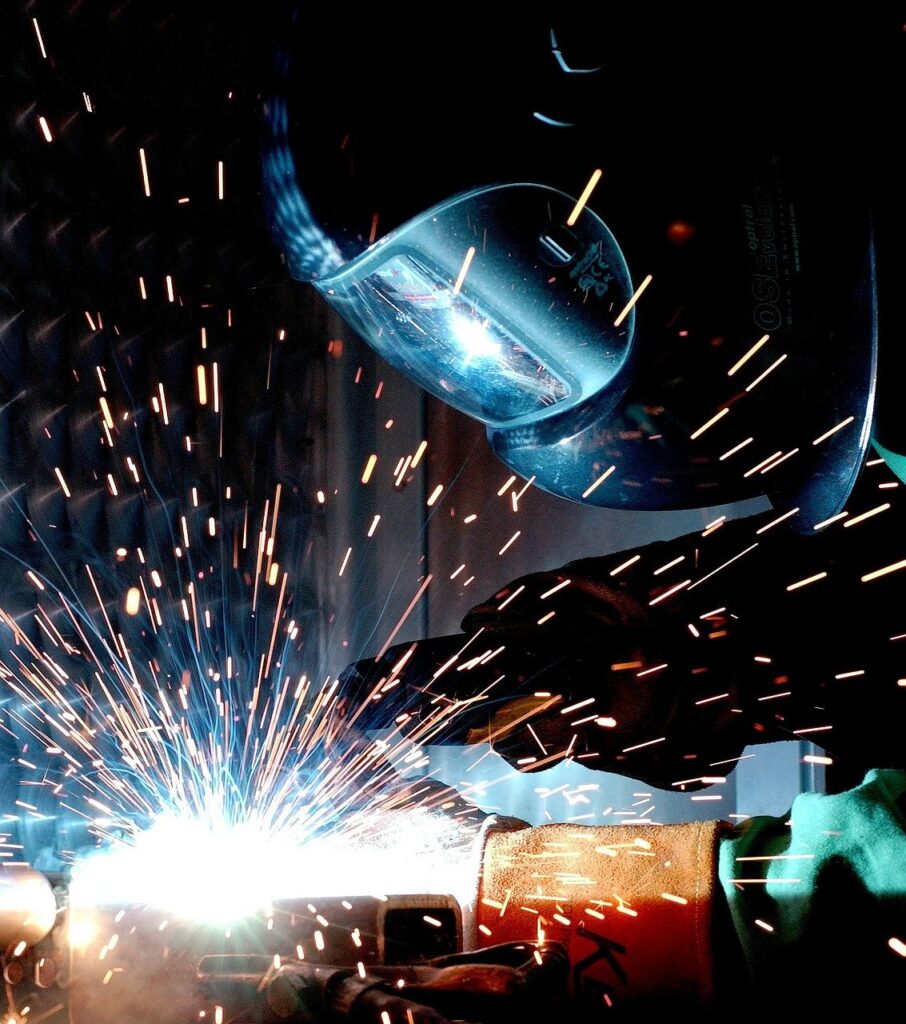
What is a Shielding Gas?
A shielding gas consists of inert or semi-inert gases that cover the weld pool and protect it from being exposed to atmospheric gases. Shielding gases are used to protect the weld surface from being oxidized by some of the harmful gases that pollute welding. These gases include
Oxygen, Carbon dioxide, Nitrogen, and Water vapour. The shielding gases are most commonly observed in Metal Inert Gas welding (MIG) and Tungsten Inert Gas Welding (TIG) processes.
The type of shielding is to be selected based on the type of welding process and the type of material to be welded. The improper choice of the shielding gas can cause porosity, poor weld, excessive spatter which consumes extra effort to remove the scattered droplets reducing the productivity of the welding. If not used carefully, these shielding gases can enter our body, displace oxygen and can be fatal to our lives.
Types of Shielding Gases
Generally, inert gases and semi-inert gases are used as shielding gases for any welding process. As the name suggests, inert gases or noble gases are chemically inert with other elements. They are colourless and odourless. They have been used in TIG or MIG welding of non-ferrous metals. Of them, argon and helium are the commonly used shielding gases. Semi-inert gases or active shield gases are used with MIG on the welding of ferrous metals. They include Oxygen, Nitrogen, Carbon-dioxide and Water Vapour.
Argon
Argon (Ar) is the most commonly used shielding gas heavier than air. It is good as shielding gas for welding in the flat position and deep groove welding. Argon plays a crucial people in maintaining arc stability resulting in improved weld penetration, greater filler wire transfer and magnified weld appearance. It is commonly used with aluminium and non-ferrous metals. The combination of Argon with helium enhances heat transfer properties whereas carbon dioxide or oxygen improves arc stability.
Helium
Helium is the oldest shielding gas used in welding. It is lighter than air and chemically inert towards molten metals. With the high thermal conductivity of helium and higher ionization potential, the gas requires a higher voltage to start the arc and provide wide and deep welds. Thus the gas is suitable for shielding aluminium, magnesium and copper alloys. It is used in laser welding and carbon dioxide lasers. Helium gas is expensive than argon and requires higher flow rates. Thus it is less economical for mass production. It is to be observed that helium produces erratic arc and enhances spatter making it unsuitable for shielding steels.
Carbon Dioxide
It is the least expensive and one of the oldest shielding gases used for welding. Carbon dioxide is the most suitable shielding gas for welding steels as it enhances weld speed, penetration and mechanical properties. However, using it produces a lot of smoke and spatter losses which can be reduced by combining it with argon. The other reason for mixing carbon dioxide with argon for shielding is that it reduces the surface tension of the molten metal. Carbon dioxide as a shielding gas is unsuitable for aluminium as it is too fragile to handle high temperatures.
Oxygen
Usage of oxygen as an addition in minor quantities along with other gases can provide effective shielding. Higher quantities of oxygen shielding can cause brittleness in the welds. About 2-5% of oxygen can be added to argon for shielding purposes. It enhances the arc stability, reduces the surface tension of the molten metal, and minimizes spatter. While using this gas for shielding, there are high chances of oxidation of the weld material. Thus, it is not suitable for welding aluminium, copper, magnesium and other metals. It increases the amount of slag formed during welding. Gradually the Argon-oxygen blends are being replaced by Argon-carbon dioxide blends for better utilisation of the shielding gas.
Conclusion
Some of the important properties of shielding gases include thermal conductivity, heat transfer properties, relative density w.r.t air, ease of ionization etc. selection of a shielding gas should depend on the above properties and the type of material being welded.