Modular welding fixtures vs Traditional
What is a Modular Welding Fixture?
The modular welding fixture comes with a flat surface table comprising machined holes to precisely hold clamps and components for seamless welding operations. They are popular for their adaptability to accommodate a broad range of components during welding operations, enhancing operator safety & work efficiency.
In the dynamic manufacturing industry where precision and efficiency play critical roles, the welding industry is undergoing a transformation driven by technological evolutions. Among the solutions driving this transformation, modular welding fixtures take center stage to meet the diverse operational needs. Today, we explore the importance of modular welding fixtures followed by highlighting the differences between modular & traditional welding fixtures.
Looking for a Modular welding fixture? Contact us
Difference Between Modular And Traditional Welding Fixtures
Given below are some of the notable differences between modular and traditional welding fixtures.
1. Functionality
Traditional Welding Fixture: Traditional welding fixtures come with fixed welding tables & are designed for specific welding purposes. These fixtures provide stable and reliable surfaces tailored to particular welding operations.
Modular Welding Fixture: The modular welding fixtures are versatile equipment & come with a table with machined holes and standard components. These components can be rearranged and securely held on the table to accommodate a wide range of operations.
The primary objective is to facilitate the assembly of components, allowing users to quickly adapt and create fixtures tailored to diverse welding tasks. The modular approach enables flexibility and efficiency in handling varying requirements without the need for fixed, task-specific setups.
2. Accuracy & Precision
Traditional Welding Fixture: Traditional welding fixtures are meticulously designed for specific purposes, providing the highest levels of accuracy and stability during designated operations. The fixed nature of these fixtures ensures precise alignment and consistent results for the intended welding tasks. However, if any adjustments are required due to changes in the project or welding requirements, it may involve more manual effort and time.
Modular Welding Fixture: Modular welding fixtures provide precise welding output due to their ease of use & versatility to accommodate various components. The flexibility of modular fixtures allows for precision in handling diverse welding tasks. By being able to rearrange and reconfigure standard components on the table, these fixtures ensure accurate and repeatable setups for different welding operations. This adaptability enhances the overall precision of the welding process, especially in environments where tasks vary and quick adjustments are necessary
3. Cost
Traditional Welding Fixture: Traditional welding fixtures are meticulously designed for specific purposes, providing the highest levels of accuracy and stability during designated operations. The fixed nature of these fixtures ensures precise alignment and consistent results for the intended welding tasks. However, if any adjustments are required due to changes in the project or welding requirements, it may involve more manual effort and time.
Modular Welding Fixture: Modular welding fixtures have a higher initial cost due to the advanced technologies involved. However, their ability to deliver high weld quality, improved productivity, and reduced labor costs often justifies the upfront investment.
4. Ease of Use
Traditional Welding Fixture: As these fixtures are designed for specific welding operations, they may not be user-friendly for everyone. They require skills and expertise to set up and operate successfully. The intricate design and fixed nature may make them less accessible to operators without specialized training.
Modular Welding Fixture: Modular welding fixtures are designed with user-friendly features, and intuitive controls, and often incorporate automation. This makes them easily operable by individuals of varying skill levels. The modular design allows for quick adjustments and adaptability, promoting accessibility for a broader range of operators.
5. Safety
Traditional Welding Fixture: Traditional welding fixtures typically come with basic safety measures. However, they may lack the integration of modern safety methods and advanced technologies. While they provide fundamental safety, additional precautions might be necessary.
Modular Welding Fixture: Whereas, the modular welding fixtures come with advanced safety features and controls, prioritizing operator safety through cutting-edge technologies. The comprehensive safety features make modular fixtures reliable for creating and maintaining a secure welding environment.
Conclusion
The capabilities of a modular welding fixture extend beyond those of a standard fixture table. Engineered for efficiency, time savings, ease of use, adaptability, and precise welding output, it offers a superior solution for diverse welding needs. For a good quality modular welding fixture, visit our Cyclotron Automation website. We accommodate a variety of modular welding fixtures to enhance safety and optimize welding operations.
Looking for a reliable Welding Tables Manufacturer?
Contact us at +91 9881217196
OR
Fill this form and our representative will get back to you.
Why Choose Cyclotron Welding tables?
- High Engineered: Cyclotron has designed the tables with high precision. While traditional flat tables may be suitable, for projects intricate welding tasks require precision in every dimension.
- 3 Workspace: With a welding table welders have a three workspace that allows them to position their workpieces with accuracy. This not only enhances the quality of the welds but also reduces the need for extensive rework.
- Highly Versatile: Whether you’re working on a small scale project or tackling scale industrial applications welding tables prove to be highly versatile because of the high accuracy of building.
- Modular design: The adjustable fixtures and modular design of these tables can accommodate workpieces of sizes and shapes. This adaptability is crucial in todays diverse welding landscape, where professionals often face a range of projects.
- Time Saving: In the welding industry time is money and investing in a welding table significantly contributes to time efficiency. The precision provided by these tables minimizes the time spent on adjustments.
- Cost Saving: Additionally by reducing rework requirements businesses can experience cost savings when utilizing tables—making them an intelligent investment choice, for optimizing welding processes.
Countries we Export to
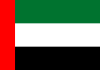
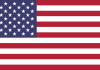
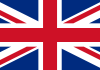
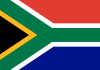
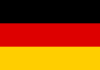
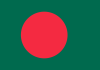
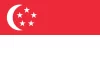
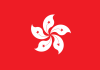
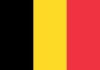
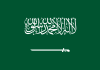
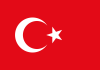
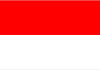
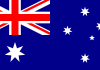
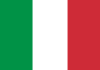
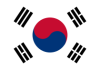
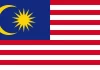

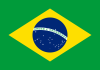
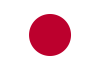
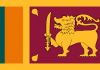
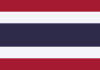
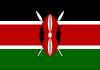
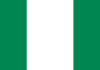
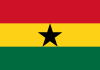