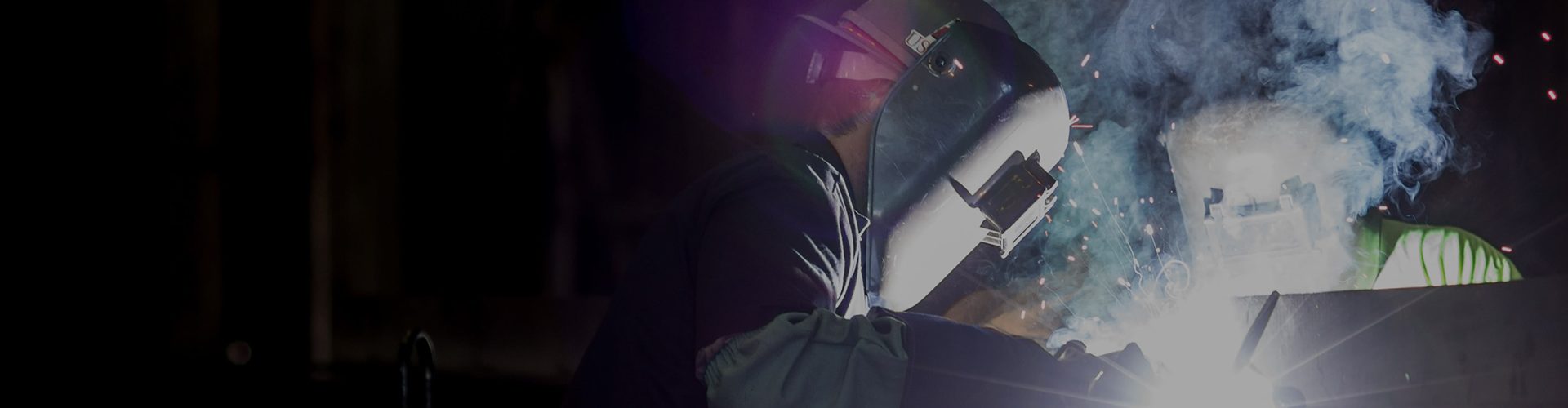
BLOGS BY CYCLOTRON
Design of welding fixtures (Guidelines & considerations)
Based on the requirements, the welding fixtures are available in different sizes and materials. In operations like welding, a high-quality product is absolutely necessary. To obtain a good product, precise fixturing is equally important. Thus, the precision and quality of the fixture play a vital role in manufacturing a component. The fixture contains locators, clamps, supports and fixture body. Fixtures must position the workpiece accurately with respect to the welding torch or measuring device or another component. It affects the weld quality, productivity and cost directly. During welding, various residual stresses are produced. These residual stresses are responsible for causing distortion. The fixture reduces this distortion and also helps in decreasing production loss, manufacturing lead time for welding.
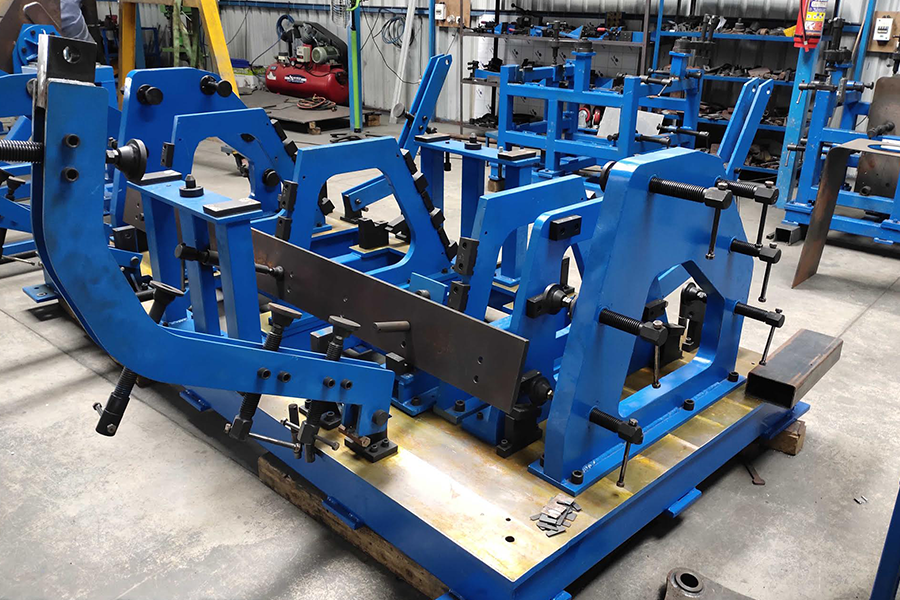
Design considerations of welding fixtures
- For high production or complex objects fixturing, some additional arrangements are required when compared to simple fixturing
- Something that can quickly get fixed into the fixture and establish a firm holding to the parts to be welded is necessary
- While welding parts of different dimensions, setup blocks are advantageous over the landing method of locating.
- These setup blocks are interchangeable to accommodate various types of workpieces.
- Some other locators like dowel pins, adjustable, spring plungers etc for locating different work parts.
- The mainframe of the fixture should be strong so that the deflection of the fixture caused by operations and clamping should be as minimum as possible. The frame should be massive enough to withstand vibration and chatter during the processes.
- Frames of the fixtures are fastened with screws or welded in case of a permanent joint. If we require frequent changing of parts, the frames are fastened with screws. If the body of the fixture has a complex shape, then it can be manufactured from cast iron.
- Clamps are chosen such that they can be accommodated quickly with minimum effort.
- All the locators should be completely visible to the operator and accessible for cleaning
- The surface area of contact should be as small as possible to avoid causing damage to the workplace due to clamping or workforces.
- The workpiece should be held firm using 3 or more support points depending on the type of the workpiece. Also, these support points should circumscribe the centre of gravity of the workpiece.
Design guidelines for Fixtures:
- Positioning of workpieces consumes time. Thus arrangements have to be made for the quick positioning and removal of the work parts to save time and improve productivity.
- The design should consider the safety of the operator and the workpiece too.
- The surfaces of fixtures are to be made of hardened materials to resist wear but are tough enough to withstand the impact forces that occur during welding.
- Sufficient clearance is to be provided for the quick loading and unloading of the workpieces.
- The fixture should be rigid enough to absorb vibrations during welding so that it doesn’t cause unnecessary movements in the tool or workpiece.
The main purpose of the fixture in the manufacturing industry is to reduce worker fatigue and improve operational safety by decreasing the efforts to hold the workpieces.
NEED A WELDING FIXTURE ?
We at Cyclotron Robotics and Automation Pvt. Ltd. manufacture all types of welding fixtures as per your requirement.